Finishing
Their purpose is to provide additional functionalities to the textile.
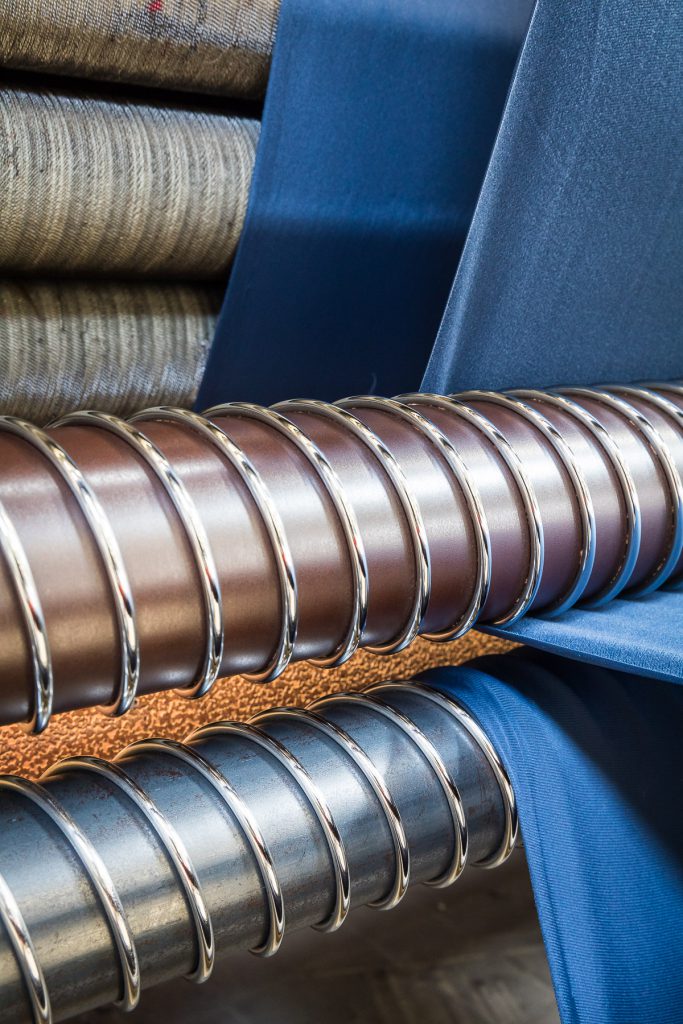
Mechanical finishes
Finishing treatments allow to modify the surface, the touch or the appearance of a textile by the physical action of machines.
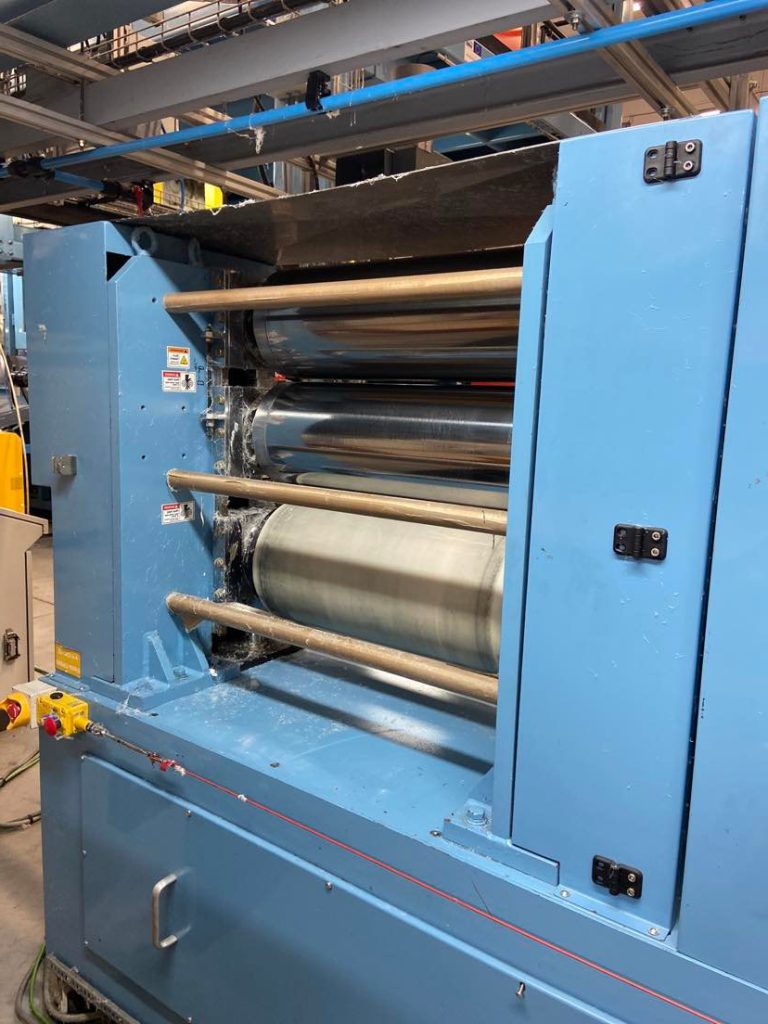
Calandrering
Passage of the textile between two cylinders of which at least one is heated, the purpose being to give shine.
- Stamping and cockling : Passage of the textile in a calender with engraved cylinders in relief (one with the wished pattern and the other with the opposite). Under the heat effect, the fabric will keep the shape of the engraving of the cylinder. Stamping is also used to draw patterns only on a part of the fabric, for this technique, one of the cylinders is engraved, and the other one is a flat cylinder.
- Laquering : Passage of the fabric in a calenders, the crushing effect of the yarns cause brightness shades.
Raising and fulling
Textile raising on the surface by needle plates in order to bring out fibrils from the fabric. These fibrils will form a kind of fluff fibers on the surface, which gives it a soft and comfortable aspect.
Grinding
Action of rubbing an emery cloth on the surface to give a “peach skin” effect.
Brushing
Passage of the fabric under the action of ceramic and carbon brushes. This technique allows a soft touch, lighter than grinding or raising.
Shearing
Action to cutting the outgoing yarns of the material by using a knife. This technique is used for velvet or suede for exemple, where the surface is shaved after shearing.
Sanforization
Application of a high quantity of steam on the textile roll, compressed by a rubber band. It is dried by a calendering. This technique is only possible on natural textiles and allows to make it unshrinkable.
Microperforation
The textile is passed over a cylinder with needles that create micro-holes. The aim is to modify the permeability, the adherence of the material, its mechanical properties and other parameters.
Chemical finishes
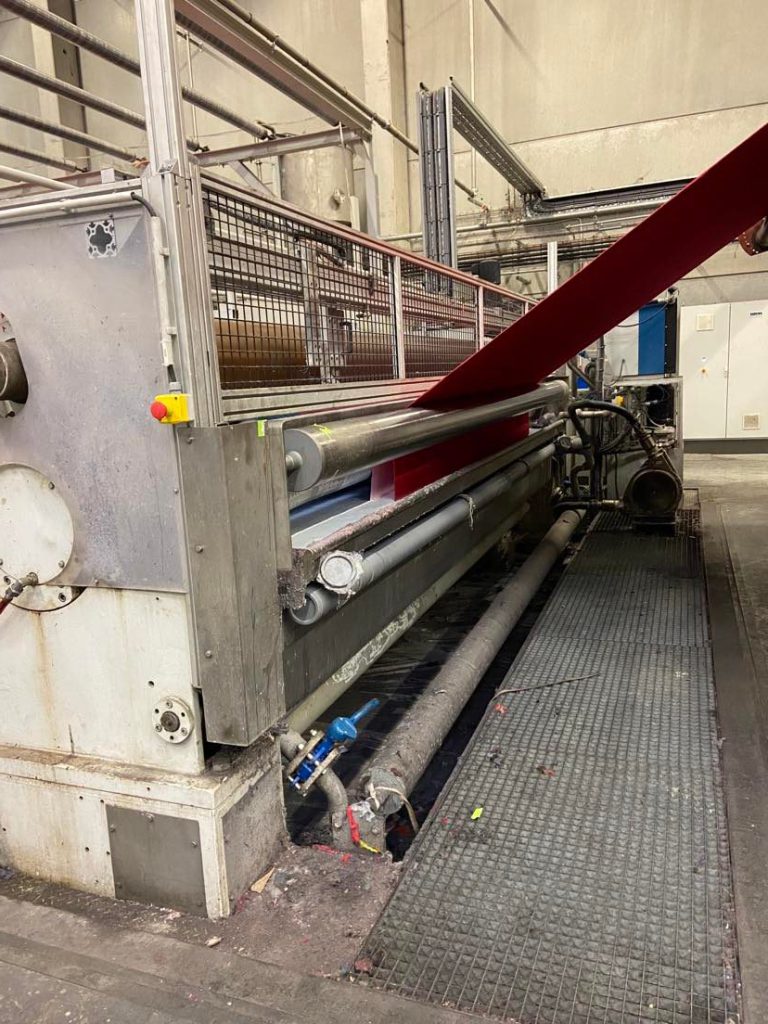
Impregnation
- Padding : The textile is passed through a solution provide the property. The textile is then passed between two squeezing rollers to eliminate the excess and make the solution penetrate the heart of the fiber. The textile will then be cross-linked in an oven (passage in an oven in order to bind the molecules of the solution with those of the textile).
- Bath depletion / Full-bath : Immersion of the textile in a bath loaded with molecules allowing to bring the functionality and wait for the loads to fix on the surface. The textile is then wrung out, rinsed, dried and cross-lincked in the oven.
- Spraying : spraying of a solvent loaded with molecules bringing the property on the textile.
Lincking
Spreading of a polymer paste, by a licker roller, on one of the textile surface. The textile is then passed in an oven to be cross-linking (passage in an oven in order to bind the molecules of the solution with those of the textile).
Coating
Deposit of a polymer paste on the surface and then pass the textile through the rolls to distribute the paste uniformly. The textile then passes through an oven to be cross-licked (passage in an oven in order to bind the molecules of the solution with those of the textile).
Micro-encapsulation
Application of micro-capsules of active ingredients on the textile by bath depletion, padding, coating or grafting. Micro-capsules are released by friction, heat or humidity.
Grafting
Grafting of active principale micro-capsules onto fibers. The compatibility between the molecules and the surface is the essential point of this technique. A grafting allows a better holding of the micro-capsules.
Low pressure plasma
Injection of an ionized gas to the textile in a vacuum chamber. It allows an increase of the surface tension of the surface. This finishing allows a better adhesion of glues and inks, a deep cleaning and a waterproofing of the textile. The plasma waterproof replaces the use of fluorine,which is toxic for the environment.