Cutting and sewing
The purpose of cutting is to separate the different parts composing a product in order to assemble it by sewing to obtain the final product.
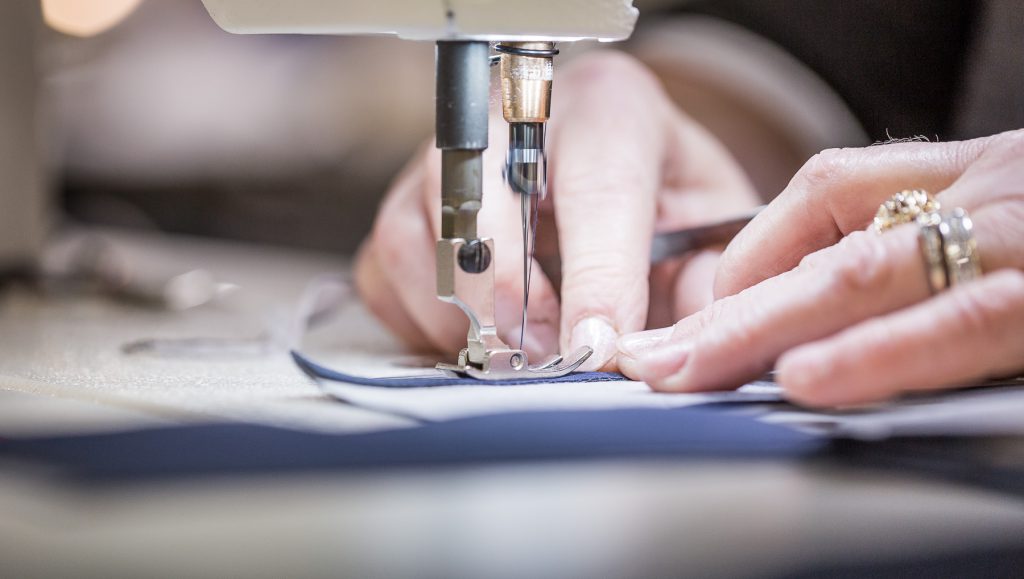
Types of cuts
Die-cutting
Cutting of plastic materials, foam and leather mainly. The die cutters are placed on the surface and then press or struck to cut the desired shapes.
Cutting on needle table
A precise cut that allows patterned textiles to be perfectly joined at the seams. This type of cut is used for repetitive and regular patterns, mainly for striped or checked garments.
Band-saw cutting
Precise cutting for thick mat by a band-saw. It can cut fabric, leather, foam, rubber, etc.
Sectioning
Straight cut allowing in particular to cut panels to constitute mat of textile.
Manual cutting
Cutting with manual scissors of all materials.
Electric or pneumatic scissor cutting
Cutting of mat of all materials with an electric or pneumatic scissor.
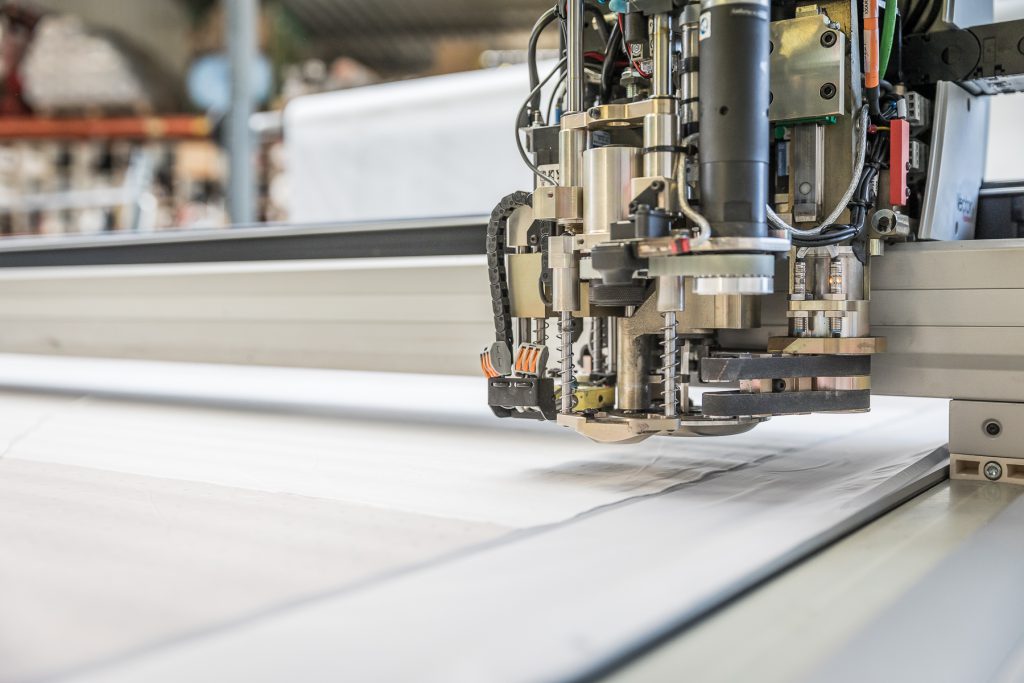
Automatic cutting
Cutting on an automated cutting table. Patterns are sent from a computer. Can be used for single layer or thin mat. A cutting head equipped with a rotatiting blade cuts the fabric while saving a maximum of material.
Laser cutting
Cutting similar to automatic cutting where a laser beam replaces the blade. The laser melts the contour of the parts and thus has clean and cauterized edges. For synthetic materials, foams and leather only.
Types of assemblies
High frequency welding
A high frequency electromagnetic field combined with a continuous pressure will heat and melt the synthetic materials to be joined. The two surfaces are pressed together during the melting process, and they will be permanently bonded. This technique avoids water infiltration at the seams and reduces the thickness of the seams which, especially for sportswear, can cause irritation. It also produces clean and precise cuts that do not require finishing. Can only be used on synthetic or partially synthetic materials.
Ultrasonic welding
Ultrasound is sent to a metal part (sonotrode) to set it in vibration. In direct contact with the thermoplastic surface (or part of it), the friction will generate heat that will melt the synthetic materials and thus bind the two surfaces. This technique avoids water infiltration at the seams and reduces the thickness of the seams which, especially for sportswear, can cause irritation. It also produces clean and precise cuts that do not require finishing. It can only be used on low melt synthetic materials.
Thermal welding
This technique consists of applying heat created by a resistor, as well as pressure on the area to be bonded. The heat will melt the plastic fabrics and the pressure will bond the two surfaces.
Mainly used for polyester which does not weld with high frequency welding.

Sewing with threads
It is the classic confection allowing the assembly of two pieces by the interweaving of at least two threads.